Шаршау сынуын бақылау және сыну механизмін талдау үшін сканерлеуші электронды микроскоп пайдаланылды; сонымен бірге сыналатын болаттың көмірсіздендіруі бар және онсыз шаршау мерзімін салыстыру және көмірсіздендірудің сыналатын болаттың шаршау өнімділігіне әсерін талдау үшін әртүрлі температурада көмірсіздендірілген үлгілерде иілу шаршау сынағы жүргізілді. Нәтижелер қыздыру процесінде тотығу мен көміртексіздендірудің бір мезгілде болуына байланысты екеуінің өзара әрекеттесуінің нәтижесінде температураның өсуімен толық көмірсізденген қабаттың қалыңдығының жоғарылау, содан кейін кему үрдісін көрсететінін көрсетеді. толық көмірсіздендірілген қабаттың қалыңдығы 750 ℃ температурада 120 мкм максималды мәнге жетеді, ал толық көмірсіздендірілген қабаттың қалыңдығы 850 ℃ температурада ең аз 20 мкм мәнге жетеді, ал сынақ болатының шаршау шегі шамамен 760 МПа, және сыналатын болаттағы шаршау сызаттарының көзі негізінен Al2O3 металл емес қосындылары болып табылады; декарбуризация әрекеті сынақ болаттың шаршау мерзімін айтарлықтай қысқартады, сыналатын болаттың шаршау өнімділігіне әсер етеді, декарбуризация қабаты неғұрлым қалың болса, шаршау мерзімі соғұрлым аз болады. Декарбуризация қабатының сынақ болатының шаршау өнімділігіне әсерін азайту үшін сынақ болатының оңтайлы термиялық өңдеу температурасын 850℃ деңгейіне орнату керек.
Тісті жабдық автомобильдің маңызды құрамдас бөлігі болып табылады,жоғары жылдамдықпен жұмыс істеуге байланысты тісті беріліс бетінің торлы бөлігі жоғары беріктік пен тозуға төзімділікке ие болуы керек, ал тіс түбірі материалға әкелетін жарықшақтарды болдырмау үшін тұрақты қайталанатын жүктемеге байланысты жақсы иілу қажу қабілетіне ие болуы керек. сыну. Зерттеулер көрсеткендей, көміртексіздену металл материалдардың айналдыру иілісі шаршау өнімділігіне әсер ететін маңызды фактор болып табылады, ал айналдыру иілісі шаршау өнімділігі өнім сапасының маңызды көрсеткіші болып табылады, сондықтан сынақ материалының көміртексіздендіру тәртібі мен иілу шаршау өнімділігін зерттеу қажет.
Бұл жұмыста, 20CrMnTi тісті болат бетін декарбюризациялау сынағы бойынша термиялық өңдеу пеші, өзгеретін заңның сынақ болат декарбюризация қабатының тереңдігі бойынша әртүрлі қыздыру температурасын талдау; QBWP-6000J қарапайым арқалықтың шаршауын сынау машинасын пайдаланып, сынақ болаттың айналмалы иілу шаршау сынағы, сынақ болаттың шаршау өнімділігін анықтау және сонымен бірге нақты өндіріс үшін сынақ болатының шаршау өнімділігіне декарбуризацияның әсерін талдау. өндіріс процесі, өнімнің сапасын арттыру және ақылға қонымды анықтама беру. Сынақ болаттың шаршау өнімділігі иілу шаршауын сынау машинасымен анықталады.
1. Сынақ материалдары мен әдістері
20CrMnTi тісті болатты қамтамасыз ететін қондырғыға арналған сынақ материалы, негізгі химиялық құрамы 1-кестеде көрсетілгендей. Декарбюризация сынағы: сынақ материалы Ф8 мм × 12 мм цилиндрлік үлгіге өңделеді, беті дақсыз жарық болуы керек. Термиялық өңдеу пеші 675 ℃, 700 ℃, 725 ℃, 750 ℃, 800 ℃, 850 ℃, 900 ℃, 950 ℃, 1 000 ℃ температураға дейін қызады, содан кейін бөлме температурасына дейін қыздырылып, ауа температурасына дейін сақталады. Үлгіні орнату, ұнтақтау және жылтырату арқылы, 4% азот қышқылының спирт ерітіндісімен эрозиясымен термиялық өңдеуден өткеннен кейін, металлургиялық микроскопияның көмегімен сынақ болатты көмірсіздендіру қабатын байқау, әртүрлі температурада декарбюризация қабатының тереңдігін өлшеу. Айналдыру иілісі шаршау сынағы: сынақ материалы екі топтың иілу шаршау үлгілерінің өңдеу талаптарына сәйкес, бірінші топ көмірсіздендіру сынағы жүргізбейді, екінші топ әртүрлі температурада көміртексіздендіру сынағы. Айналдыру иілісі шаршауды сынау машинасын пайдалану, иілу шаршау сынау үшін сынақ болаттың екі тобы, сынақ болаттың екі тобының шаршау шегін анықтау, сынақ болаттың екі тобының шаршау мерзімін салыстыру, сканерлеуді қолдану электронды микроскоппен шаршау сынуын бақылау, үлгінің сыну себептерін талдау, сыналатын болаттың шаршау қасиеттерін көміртексіздендіру әсерін зерттеу.
1-кесте Сыналатын болаттың химиялық құрамы (массалық үлесі) салмағы %
Қыздыру температурасының көміртексіздендіруге әсері
Әртүрлі қыздыру температураларында көміртексіздендіруді ұйымдастырудың морфологиясы 1-суретте көрсетілген. Суреттен көрініп тұрғандай, температура 675 ℃ болғанда үлгінің бетінде декарбюризация қабаты пайда болмайды; температура 700 ℃ дейін көтерілгенде, жұқа ферритті декарбюризация қабаты үшін үлгі бетінің декарбюризация қабаты пайда бола бастады; температура 725 ℃ дейін көтерілгенде, үлгі бетінің декарбуризация қабатының қалыңдығы айтарлықтай өсті; 750 ℃ декарбуризация қабатының қалыңдығы максималды мәнге жетеді, бұл уақытта феррит дәні айқынырақ, өрескел болады; температура 800 ℃ дейін көтерілгенде, декарбуризация қабатының қалыңдығы айтарлықтай төмендей бастады, оның қалыңдығы 750 ℃ жартысына дейін төмендеді; температура 850 ℃ дейін көтерілуін жалғастырғанда және декарбуризацияның қалыңдығы 1-суретте көрсетілген. 800 ℃, толық декарбюризация қабатының қалыңдығы айтарлықтай төмендей бастады, оның қалыңдығы жартысы болғанда 750 ℃ дейін төмендеді; температура 850 ℃ және одан жоғары көтерілуін жалғастырған кезде, сынақ болатының толық декарбюризация қабатының қалыңдығы төмендей береді, жартылай декарбюризация қабатының қалыңдығы толық декарбюризация қабатының морфологиясы жойылғанша, жартысы декарбуризация қабатының морфологиясы біртіндеп тазаланғанша біртіндеп арта бастады. Температураның жоғарылауымен толығымен декарбюризацияланған қабаттың қалыңдығы алдымен ұлғайғанын, содан кейін азайғанын көруге болады, бұл құбылыстың себебі қыздыру процесіндегі үлгінің бір мезгілде тотығу және көміртексіздену тәртібімен байланысты, тек кезде ғана декарбуризация жылдамдығы тотығу жылдамдығынан жылдамырақ болса декарбуризация құбылысы пайда болады. Қыздырудың басында толық көміртектіден тазартылған қабаттың қалыңдығы температураның жоғарылауымен толық көмірсізденген қабаттың қалыңдығы максималды мәнге жеткенше біртіндеп артады, осы уақытта температураны көтеруді жалғастыру үшін үлгінің тотығу жылдамдығы жоғарырақ болады. толық декарбюризацияланған қабаттың жоғарылауын тежейтін декарбюризация жылдамдығы, нәтижесінде төмендеу тенденциясы. 675 ~ 950 ℃ диапазонында 750 ℃ температурада толық көмірсіздендірілген қабаттың қалыңдығының мәні ең үлкен, ал 850 ℃ температурада толық көмірсіздендірілген қабат қалыңдығының мәні ең аз екенін көруге болады, сондықтан сынақ болатының қыздыру температурасы 850℃ болуы ұсынылады.
1-сурет 1 сағат бойы әртүрлі қыздыру температурасында ұсталатын сынақ болаттың көмірсізденген қабатының гистоморфологиясы
Жартылай көміртексіздендірілген қабатпен салыстырғанда, толық көмірсіздендірілген қабаттың қалыңдығы материалдың қасиеттеріне айтарлықтай теріс әсер етеді, ол материалдың беріктігін, қаттылығын, тозуға төзімділігін және шаршау шегін азайту сияқты механикалық қасиеттерін айтарлықтай төмендетеді. және т.б., сонымен қатар сызаттарға сезімталдықты арттырады, дәнекерлеу сапасына әсер етеді және т.б. Сондықтан толық көміртексіздендірілген қабаттың қалыңдығын бақылау өнімнің өнімділігін жақсарту үшін үлкен маңызға ие. 2-суретте толық көмірсіздендірілген қабат қалыңдығының температурамен өзгеру қисығы көрсетілген, ол толық көмірсіздендірілген қабат қалыңдығының вариациясын анағұрлым анық көрсетеді. Суреттен толық көмірсіздендірілген қабаттың қалыңдығы 700 ℃ температурада шамамен 34 мкм болатынын көруге болады; температураның 725 ℃ дейін көтерілуімен толық көмірсіздендірілген қабаттың қалыңдығы 86 мкм-ге дейін айтарлықтай артады, бұл 700 ℃ температурада толық көмірсіздендірілген қабаттың қалыңдығынан екі еседен астам; температура 750 ℃ дейін көтерілгенде, толық көмірсіздендірілген қабаттың қалыңдығы Температура 750 ℃ дейін көтерілгенде, толық көмірсіздендірілген қабаттың қалыңдығы 120 мкм максималды мәнге жетеді; Температураның көтерілуін жалғастырған кезде толық көмірсізденген қабаттың қалыңдығы күрт төмендей бастайды, 800℃ температурада 70 мкм дейін, содан кейін 850 ℃ температурада шамамен 20 мкм ең төменгі мәнге дейін.
Сурет 2 Әртүрлі температурадағы толық көмірсіздендірілген қабаттың қалыңдығы
Декарбюризацияның иілу кезінде шаршау көрсеткіштеріне әсері
Декарбюризацияның серіппелі болаттың шаршау қасиеттеріне әсерін зерттеу үшін екі топ иілу шаршау сынағы жүргізілді, бірінші топ - көміртексіздендірусіз тікелей шаршауды сынау, ал екінші топ - бірдей кернеуде көміртексіздендіруден кейін шаршауды сынау. деңгейінде (810 МПа) және декарбуризация процесі 700-850 ℃ температурада 1 сағат бойы жүргізілді. Үлгілердің бірінші тобы 2-кестеде көрсетілген, бұл серіппелі болаттың шаршау мерзімі.
Үлгілердің бірінші тобының шаршау мерзімі 2-кестеде көрсетілген. 2-кестеден көрініп тұрғандай, көміртексіздендірусіз сынақ болат 810 МПа-да тек 107 циклге ұшыраған және сыну орын алған жоқ; кернеу деңгейі 830 МПа-дан асқанда, үлгілердің кейбіреулері бұзыла бастады; кернеу деңгейі 850 МПа-дан асқанда, шаршау үлгілерінің барлығы сынған.
2-кесте Әр түрлі стресс деңгейлеріндегі шаршау мерзімі (декарбуризациясыз)
Шаршау шегін анықтау үшін сыналатын болаттың шаршау шегін анықтау үшін топтық әдіс қолданылады, ал мәліметтерді статистикалық талдаудан кейін сыналатын болаттың шаршау шегі шамамен 760 МПа; сыналатын болаттың әртүрлі кернеулер кезінде шаршау мерзімін сипаттау үшін 3-суретте көрсетілгендей SN қисығы сызылады. 3-суреттен көрініп тұрғандай, әртүрлі кернеу деңгейлері шаршау мерзімі 7 болған кезде әртүрлі шаршау мерзіміне сәйкес келеді. , 107 циклдер санына сәйкес келеді, бұл үлгі осы шарттарда күй арқылы өтетінін білдіреді, сәйкес кернеу мәнін шаршау күші мәні ретінде жуықтауға болады, яғни 760 МПа. Материалдың қажу мерзімін анықтау үшін S - N қисығының маңызды анықтамалық мәні бар екенін көруге болады.
Сурет 3 Тәжірибелік болат айналмалы иілу шаршау сынағының SN қисығы
Үлгілердің екінші тобының шаршау мерзімі 3-кестеде көрсетілген. 3-кестеден көрініп тұрғандай, сыналатын болатты әртүрлі температурада көмірсіздендіруден кейін циклдар саны анық азаяды және олар 107-ден асады және барлығы шаршау үлгілері сынған және шаршау мерзімі айтарлықтай қысқарады. Жоғарыда көрсетілген көміртексіздендірілген қабат қалыңдығымен температураның өзгеру қисығын көруге болады, 750 ℃ декарбюризацияланған қабат қалыңдығы шаршау мерзімінің ең төменгі мәніне сәйкес келетін ең үлкен болып табылады. 850 ℃ декарбюризацияланған қабаттың қалыңдығы ең аз болып табылады, бұл шаршау өмірінің мәніне сәйкес салыстырмалы түрде жоғары. Декарбюризация әрекеті материалдың шаршау өнімділігін айтарлықтай төмендететінін көруге болады, ал декарбюризацияланған қабат неғұрлым қалың болса, шаршау мерзімі соғұрлым аз болады.
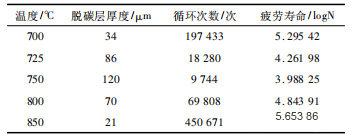
3-кесте. Әртүрлі декарбюризация температураларындағы шаршау мерзімі (560 МПа)
Үлгінің шаршау сыну морфологиясы 4-суретте көрсетілгендей сканерлеуші электрондық микроскоп арқылы бақыланды. 4(а) суретте жарықтар көзі аймағы үшін көзді табу үшін шаршау доғасына сәйкес анық шаршау доғасын көруге болады. шаршау, «балық көзінің» металл емес қосындылары үшін жарықтар көзі көрінуі мүмкін, кернеуді тудыратын жеңіл концентрациядағы қосындылар, нәтижесінде шаршау жарықтары; 4(б)-суретте жарықшықтың ұзару аймағының морфологиясы бойынша айқын шаршау жолақтарын көруге болады, өзен тәрізді таралу болды, квазидиссоциативті сынықтарға жатады, жарықтар кеңейіп, сайып келгенде сынуға әкеледі. 4(б) суретте жарықшақтың кеңею аймағының морфологиясы көрсетілген, айқын шаршау жолақтары квази-диссоциативті сынықтарға жататын өзен тәрізді таралу түрінде және жарықтардың үздіксіз кеңеюімен, сайып келгенде, сынуға әкеледі. .
Шаршау сынықтарын талдау
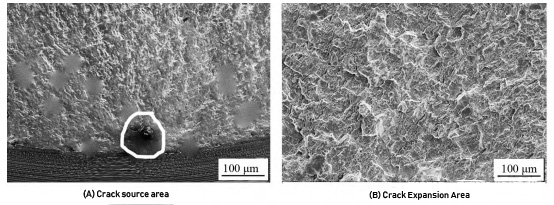
Сурет 4 Тәжірибелік болаттың шаршау сыну бетінің SEM морфологиясы
4-суреттегі қосындылардың түрін анықтау үшін энергия спектрінің құрамын талдау жүргізілді, ал нәтижелер 5-суретте көрсетілген. Бейметалдық қосындылар негізінен Al2O3 қосындылары екенін көруге болады, бұл қосындылардың қосындыларын көрсетеді. қосындылардың крекингінен туындаған жарықтардың негізгі көзі болып табылады.
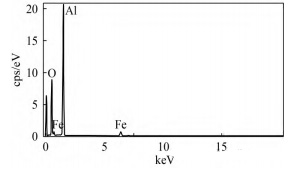
5-сурет Металл емес қосындылардың энергетикалық спектроскопиясы
Қорытындылау
(1) Қыздыру температурасын 850 ℃-ге қою шаршау өнімділігіне әсерін азайту үшін көмірсіздендірілген қабаттың қалыңдығын барынша азайтады.
(2) Сынақ болаттың иілу иілуінің шаршау шегі 760 МПа.
(3) Металл емес қосындыларда, негізінен Al2O3 қоспасында болаттың сынуы.
(4) декарбюризация сынақ болаттың шаршау мерзімін айтарлықтай қысқартады, декарбуризация қабаты неғұрлым қалың болса, шаршау мерзімі соғұрлым аз болады.
Жіберу уақыты: 21 маусым-2024 ж